1. Epoxy Didn’t Cure
Your resin and hardener could be off ratio
- Too much or too little hardener will affect the cure time and thoroughness of the cure.
- Remove the uncured epoxy. Do not apply additional material over non-curing epoxy. See Clean Up & Removing.
- Check that you’re using the correct number of pump strokes: Use equal strokes of epoxy resin and hardener. DO NOT add extra hardener for a faster epoxy cure!
- Check for correct pump (5:1 or 3:1 ratio) and pump group size (Group B epoxy resin and Group B epoxy hardener).
- Check epoxy pump ratio (see 300 Mini Pump Instructions). See Dispensing & Mixing.
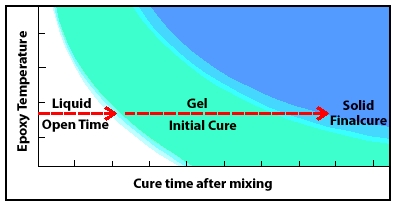
The temperature might be too low
- Allow epoxy extra curing time in cool weather.
- Apply heat to maintain the epoxy’s chemical reaction and speed the cure.
- Next time, use 205 Fast Hardener®, designed to cure with epoxy resin at lower temperatures.
- See Cold-Temperature Bonding.
The resin and hardener weren’t blended thoroughly
- Remove the uncured epoxy. Do not apply additional material over non-curing epoxy. See Clean Up & Removing.
- Mix epoxy resin and hardener together thoroughly to avoid resin-rich and hardener-rich areas. See Dispensing & Mixing.
- Only add fillers or additives after epoxy resin and hardener have been thoroughly mixed.
Incompatible epoxy products were used
- Scrape away the uncured epoxy to remove it. Do not apply additional material over non-curing epoxy. See Clean Up & Removing.
- Check the compatibility of epoxy resin and hardener. Epoxy resin will not cure properly with other brands of epoxy hardener or with polyester catalysts.
2. Epoxy Bond Failed
Insufficient cure.
See my epoxy hasn’t cured (above)...
Resin starved joint: epoxy has wicked into porous surfaces leaving a void at the joint.
Wet out bonding surfaces with a neat epoxy mixture before applying thickened epoxy. Re-wet very porous surfaces and end grain. See Bonding & Clamping.
Contaminated epoxy bonding surface.
Clean and sand the surface following the procedure in the Surface Preparation. Sand wood surfaces after planing or joining.
The bonding area is too small for the load on the joint.
Increase bonding area by adding epoxy fillets, bonded fasteners or scarf joints. See Bonding & Clamping.
Too much clamping pressure squeezed epoxy out of the joint.
Use just enough clamping pressure to squeeze a small amount of epoxy from the joint. See Bonding & Clamping.
3. Clear coating turned cloudy
Moisture from condensation or very humid conditions reacts with components in the uncured epoxy hardener.
- Apply moderate heat to partially cured epoxy coating to remove moisture and complete cure. See Out-Gassing caution in Epoxy Chemistry.
- Use 207 Special Clear Hardener® for clear coating applications and for bonding thin veneers where epoxy may bleed through to the surface.
Air is entrapped in the epoxy from aggressive roller application.
- Apply epoxy coating at warmer temperatures–epoxy is thinner at warmer temperatures.
- Apply epoxy in thin coats.
- Apply moderate heat to release trapped air from epoxy and complete cure. See Out-Gassing caution in Epoxy Chemistry.
4. Waxy Film
It’s called amine blush and it is a normal byproduct of epoxy cure in certain conditions. It’s water-soluble and easily removed.
- Remove with water. See Special Preparation—Cured Epoxy in Surface Preparation.
- Next time, use 207 Special Clear Hardener. 207 is blush-free.
5. Old Hardener Turned Red, is it Still Good?
Yes!
Some hardeners will redden in metal containers, especially where moisture is present. The red (or brown or purple) color is a normal condition. It will not affect epoxy handling or cured strength. Avoid using for clear coating or exposed areas where color is not desired.
6. Cold Temperature Application
- Apply the epoxy coating at a warmer temperature.
- Warm the epoxy resin and hardener before mixing to speed the cure in cool weather.
- Switch to a faster hardener such as 205 Fast Hardener if possible.
- See Controlling Cure Time under Epoxy Chemistry.
7. Fairing Compound Hard to Sand
Your fairing mixture is not thick enough.
- Add more filler to the epoxy mixture until it reaches a “peanut butter” consistency; the more filler added, the stiffer and easier it will be to sand.
- Allow the wet-out coat of epoxy to gel before applying the fairing material to vertical surfaces.
- See Fairing.
8. Paint or Varnish Not Drying Over Epoxy
The epoxy hasn’t fully cured.
Allow the final epoxy coat to cure thoroughly. Allow several days if necessary for slow hardeners at cooler temperatures. Apply moderate heat to complete the cure if necessary. See Controlling Cure Time under Epoxy Chemistry.
The paint or varnish is incompatible with epoxy.
- Use a different type of paint or varnish. Some paints and varnishes may be incompatible with some hardeners. If unsure, test for compatibility on a coated piece of scrap material.
- Use 207 Special Clear Hardener. It is compatible with most paints and varnishes.
The cured epoxy surface wasn’t thoroughly prepared.
Remove any amine blush and sand the epoxy surface thoroughly before applying paints or varnishes. See Final Surface Prep.
9. Epoxy Got Hot, Cured Too Quickly
Epoxy cures by exothermic (heat) reaction. Here are some reasons it can overheat:
The epoxy batch was too large.
- Mix smaller batches of epoxy.
- Transfer the epoxy mixture to a container with more surface area immediately after mixing.See Understanding Cure Time under Epoxy Chemistry, and Dispensing & Mixing.
The temperature was too warm for the hardener.
In very warm weather, use 206 Slow Hardener® or 209 Extra Slow Hardener® with 105 Epoxy Resin®.
The epoxy was applied too thick.
For thicker epoxy applications such as epoxy casting, build up several thin layers of epoxy.
10. Bubbles in Epoxy Coating
Air is entrapped in the epoxy coating. Air can easily escapes in the epoxy as the temperature of the epoxied surface rises. This is called outgassing.
- To prevent outgassing, coat wood with epoxy as the temperature is dropping—after warming the wood with heaters or during the later part of the day.
- Apply a thinner epoxy coat, allowing air to escape easier.
- Tip-off the epoxy coating with a roller cover brush to break bubbles. See Barrier Coating.
- See Out-Gassing caution in Epoxy Chemistry or read more about bubble-free coating at Epoxyworks.com.
11. Pinholes in Epoxy Coating
Surface tension can cause the epoxy film to pull away and form pinholes before it gels.
To fill pinholes, apply epoxy with an 800 Roller Cover, then for the epoxy into pinholes with a stiff plastic spreader held at a low angle. Re-coat and tip-off coating after all the pinholes are filled.
12. Fish-Eyeing in Epoxy Coating
Fish-eyeing happens when the coating surface is contaminated or improperly abraded.
- Be sure the epoxy mixing equipment is clean. Avoid waxed mixing containers.
- Be sure the surface is properly prepared and contaminate-free. Use proper grit sandpaper for the coating, e.g., 80-grit for epoxy. See the paint or varnish manufacturer’s instructions for proper surface preparation. After the surface is prepared, avoid contamination—fingerprints, exhaust fumes, rags with fabric softener (silicone). Coat within hours of preparation. After wet sanding, rinse water should sheet without beading (beading indicates contamination). Wipe with appropriate solvent and re-rinse until rinse water no longer beads.